AI-Powered Sheet Metal Works for Precision Components
Our AI manages every step of the sheet metal working process, delivering high-quality parts faster and more efficiently than ever.
AI-Powered CNC Machining for Ultimate Precision and Performance
Our AI manages every step of the CNC machining process, delivering high-tolerance parts with superior surface finishes faster and more efficiently than ever.
End-to-End Production Management
Requirement Capturing
Material & Process Selection
Design for Sheet
Metal Works
Project
Monitoring
Follow-ups & Reporting
Quality
Assurance
Risk
Analysis
Finishing
Coordination
End-To-End Production Management
Our proprietary AI platform enhances every aspect of the production process with intelligent optimization and real-time adaptability
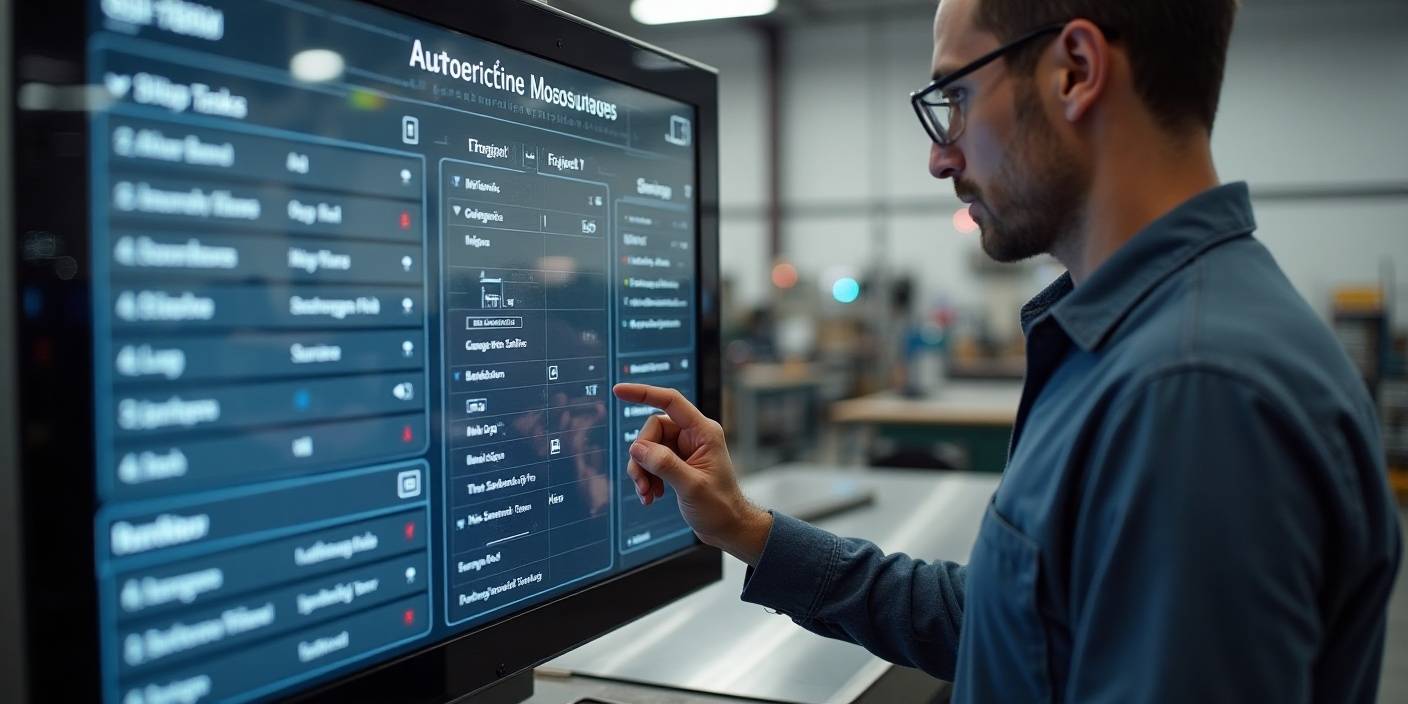
Requirement
Capturing
Our AI captures your project specifications through an intuitive interface, ensuring material selection, gauge thickness, tolerances, and surface finish requirements are understood from the start. Automatic feature recognition and fabrication strategy selection
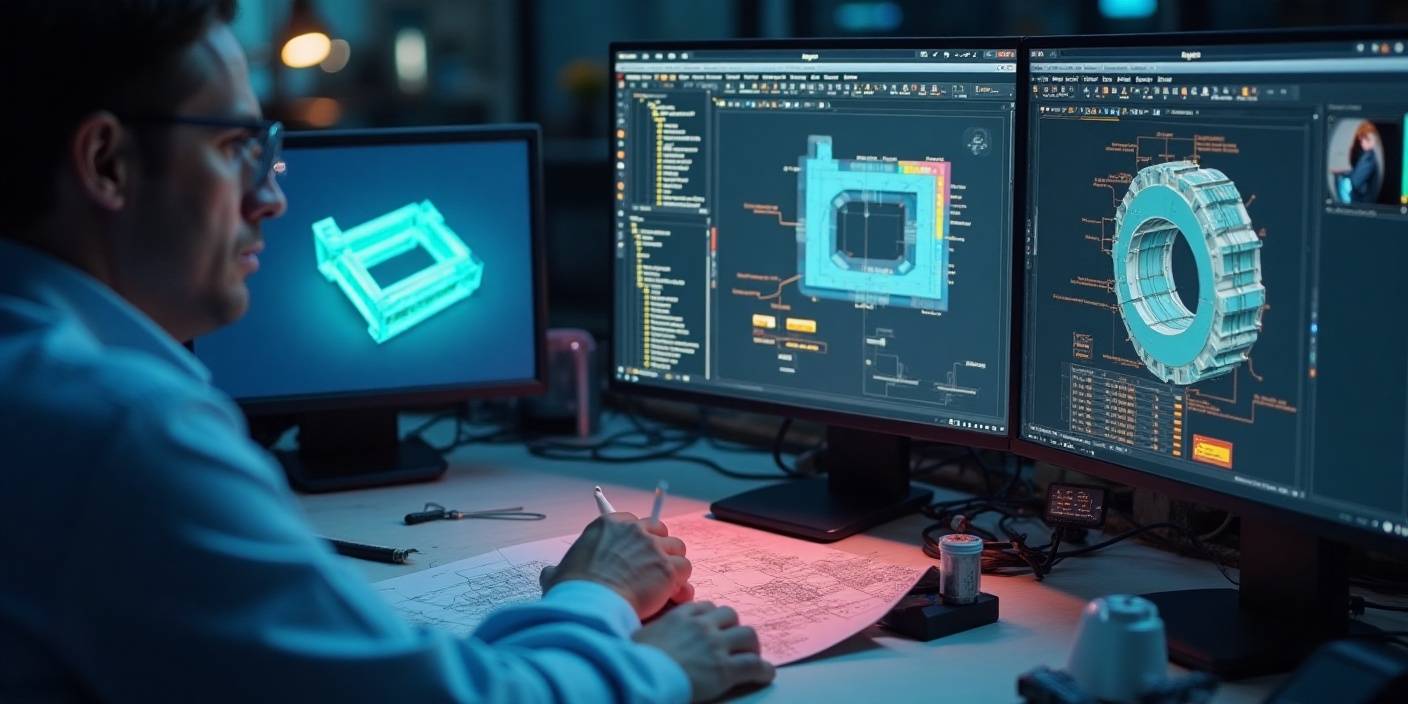
Design for
Fabrication
The AI optimizes your design for sheet metal processes, analyzing features for manufacturability, bend allowances, and potential fabrication challenges. Real-time DFM with bend relief analysis and corner treatment optimization
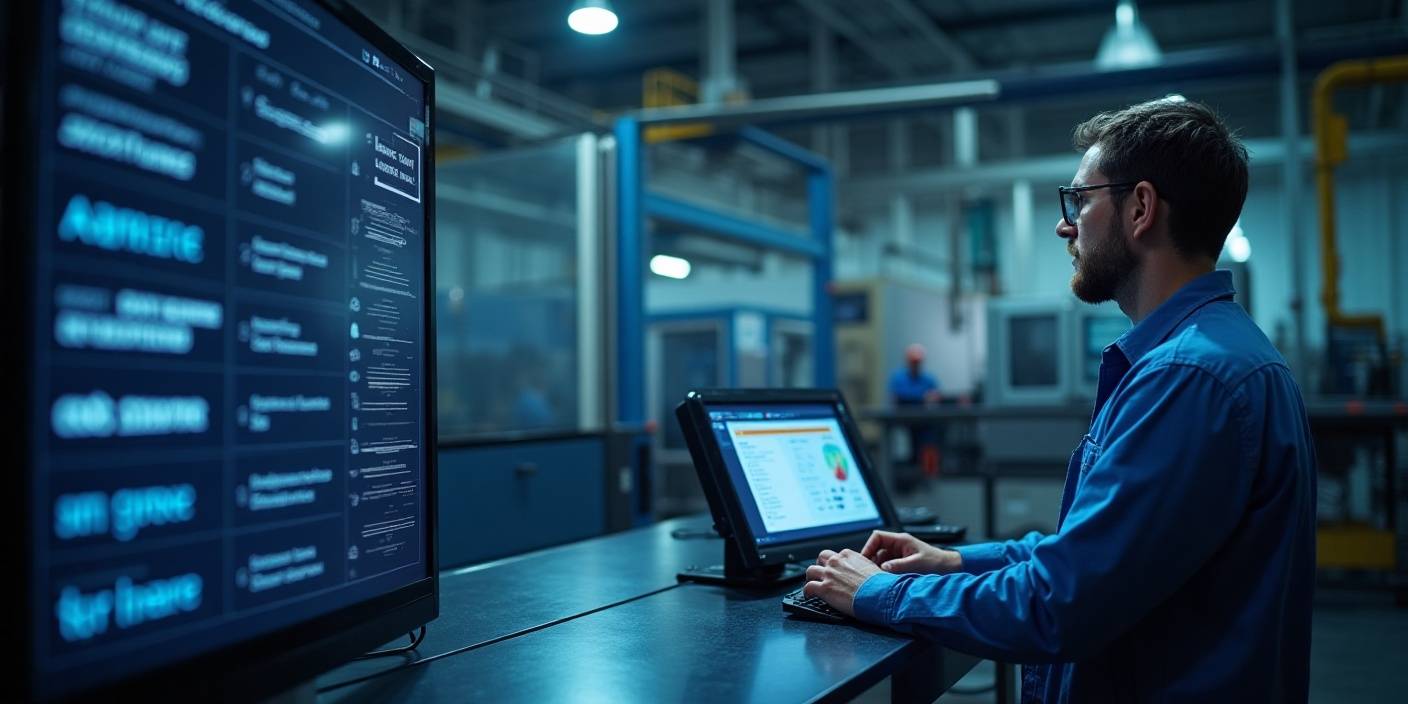
Material & Process
Selection
Our AI selects the optimal fabrication processes—laser cutting, punching, bending, welding, or forming—based on part geometry, material properties, and production volume. Intelligent tooling selection and fabrication sequence optimization
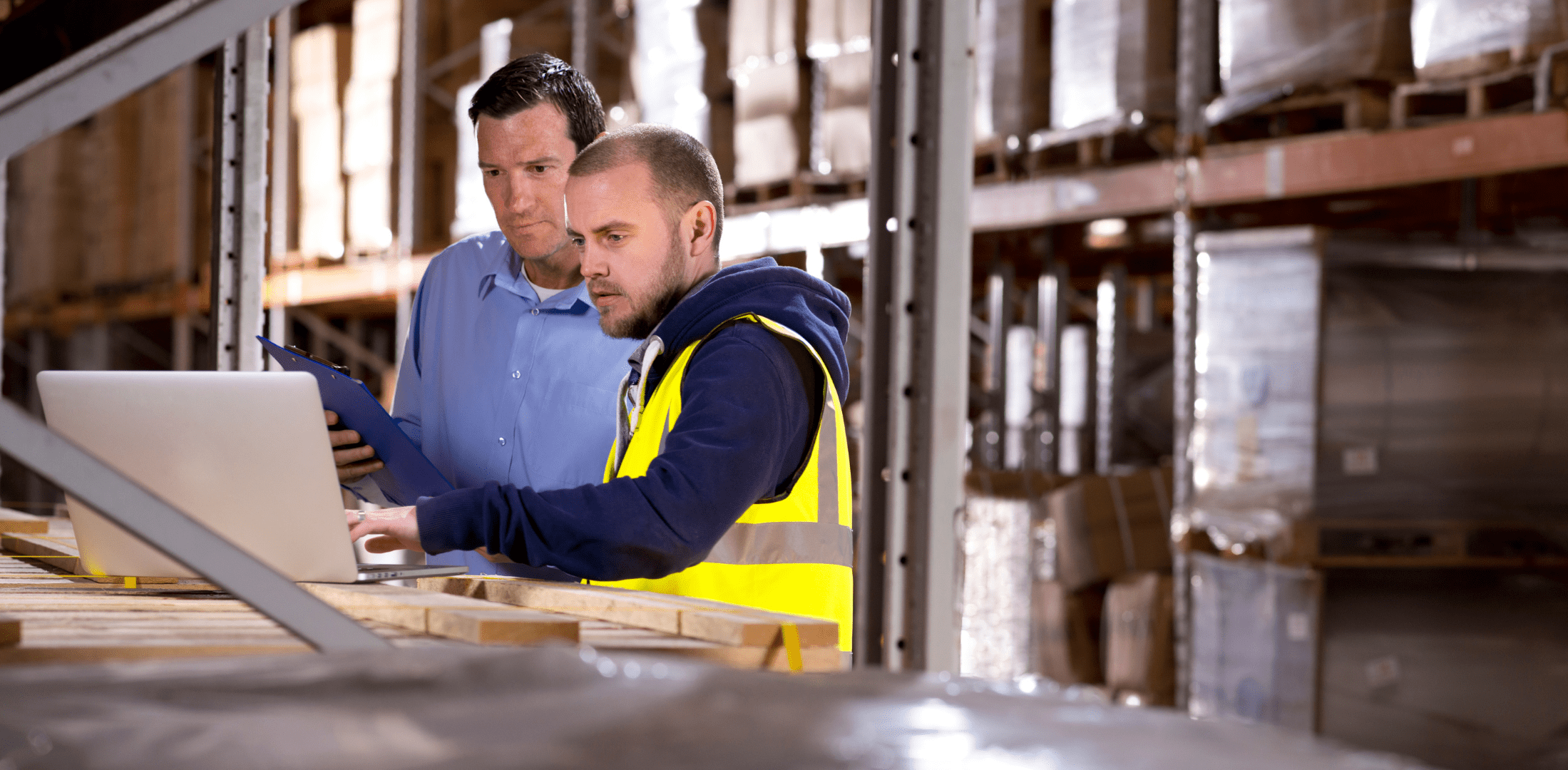
Project
Monitoring
Track fabrication operations in real-time with AI-powered updates on cutting quality, bend accuracy, and dimensional conformity. Live monitoring of forming operations and material handling
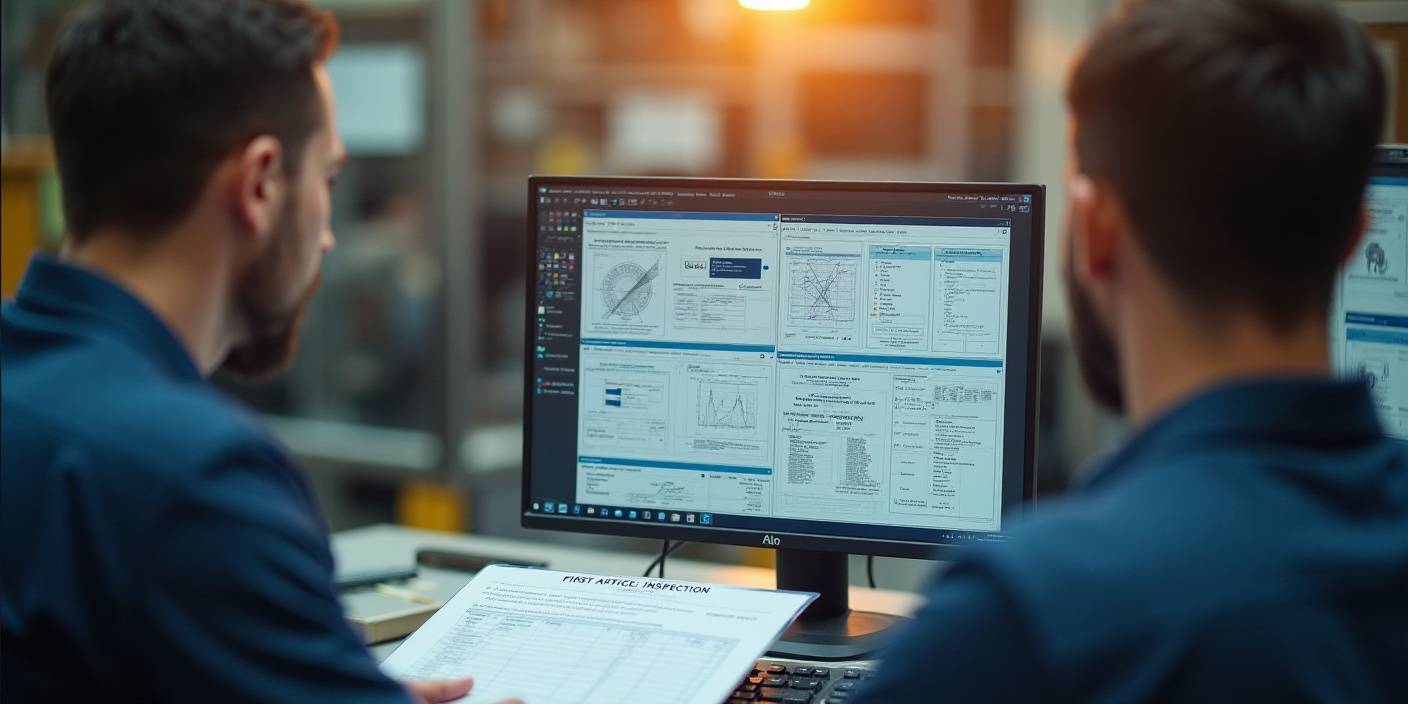
Follow-ups &
Reporting
Stay informed with automated follow-ups and detailed reports on material certification, dimensional inspection, and finish verification. Comprehensive first article inspection documentation
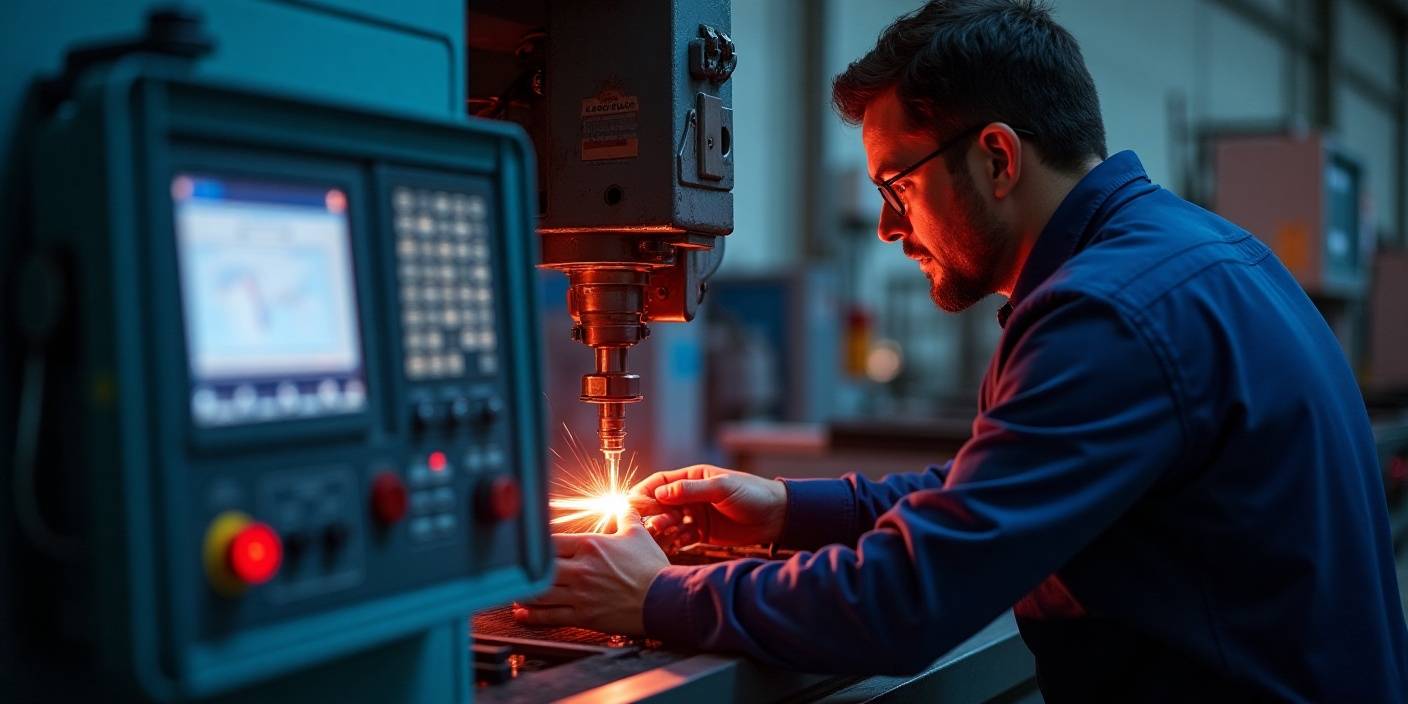
Risk
Analysis
The AI identifies fabrication risks like springback, warp, or material thinning and implements compensating strategies proactively. Predictive bend compensation and forming pressure adjustments
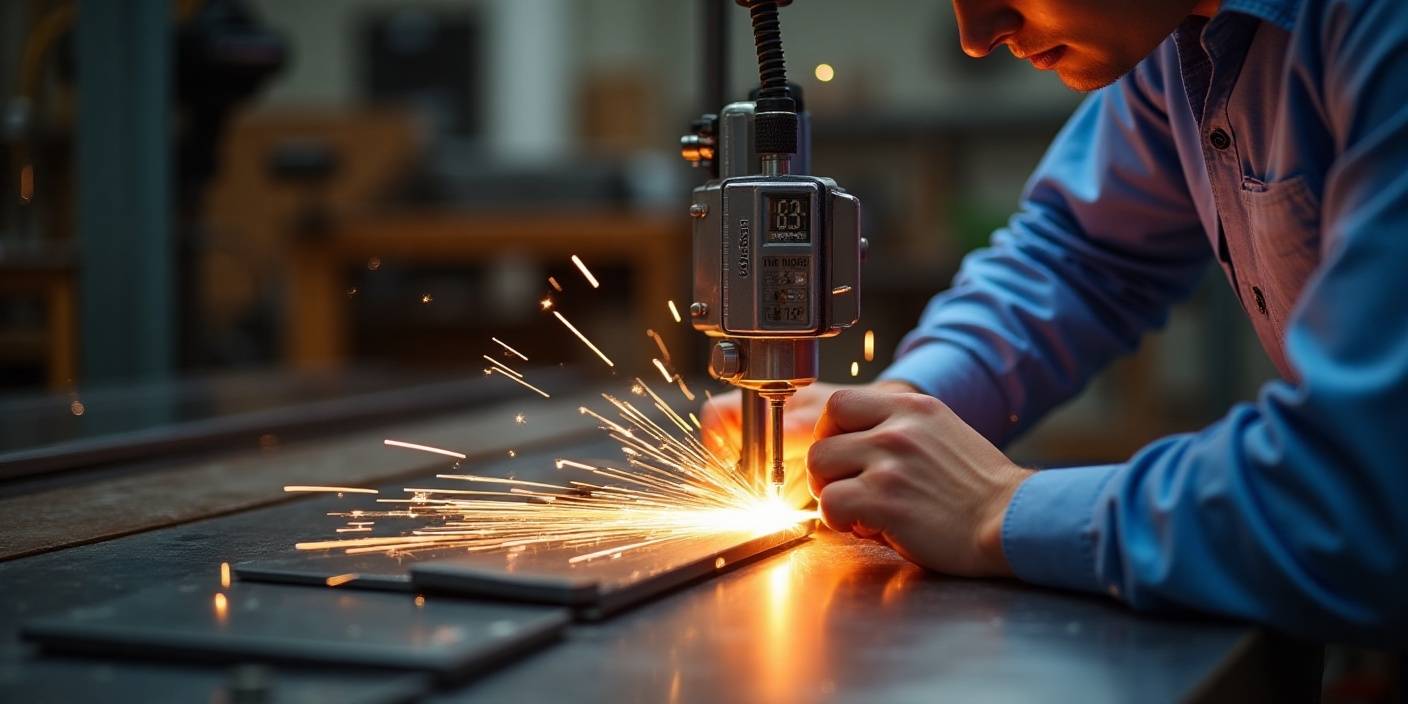
Quality
Assurance
AI coordinates dimensional inspection and surface finish verification, ensuring parts meet specifications with minimal deviation. Automated flatness inspection and edge quality validation
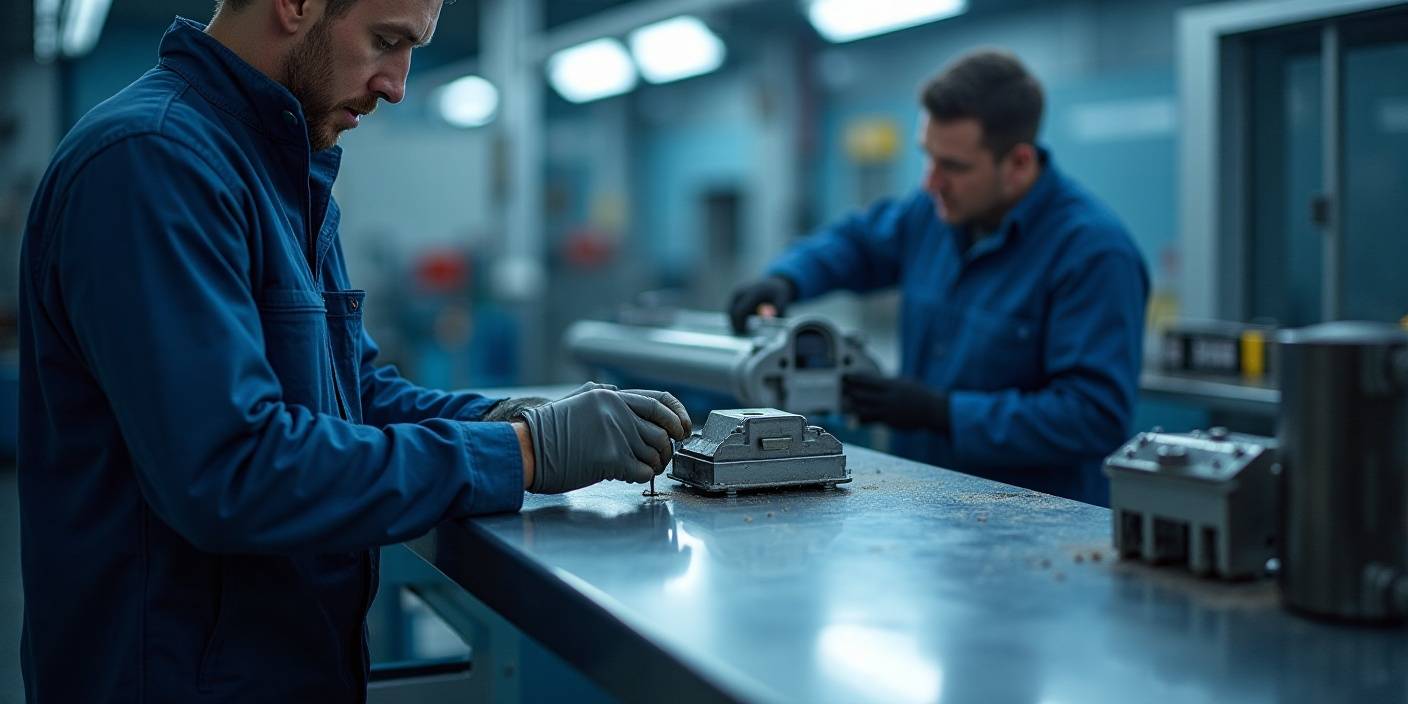
Finishing
Coordination
From deburring and edge breaking to powder coating and hardware installation, the AI optimizes the post-fabrication workflow for speed and cost. Seamless coordination of secondary operations

Material & Process
Selection
Our AI selects the optimal fabrication processes—laser cutting, punching, bending, welding, or forming—based on part geometry, material properties, and production volume. Intelligent tooling selection and fabrication sequence optimization
24/7 Availability
Our AI never sleeps, managing your project anytime, anywhere.
Unmatched Efficiency
Faster decisions and processes mean shorter lead times.
Precision & Accuracy
AI eliminates errors, delivering consistent quality.
Cost Savings
Automation cuts overhead, offering you competitive pricing.
Proactive Solutions
Risks are spotted and solved before they become problems.
Why Choose Our
AI Platform
Working with a manufacturing partner who understands your hardware needs makes all the difference.
24/7 Availability
Our AI never sleeps, managing your project anytime, anywhere.
Unmatched Efficiency
Faster decisions and processes mean shorter lead times.
Precision & Accuracy
AI eliminates errors, delivering consistent quality.
Cost Savings
Automation cuts overhead, offering you competitive pricing.
Proactive Solutions
Risks are spotted and solved before they become problems.
Human Expertise When You Need It
Our experts complement AI capabilities with specialized knowledge and hands-on experience.
- Complex project consultation and custom solutions design
- Technical support for specialized materials and finishing requirements
- Quality assurance reviews for critical applications
- On-demand engineering support and design optimization
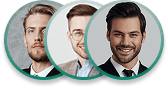
20+ Years Combined Experience
Meet Our Sheet Metal Specialists
Our Gallery
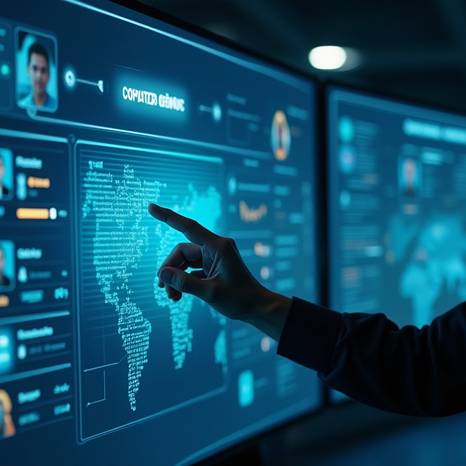
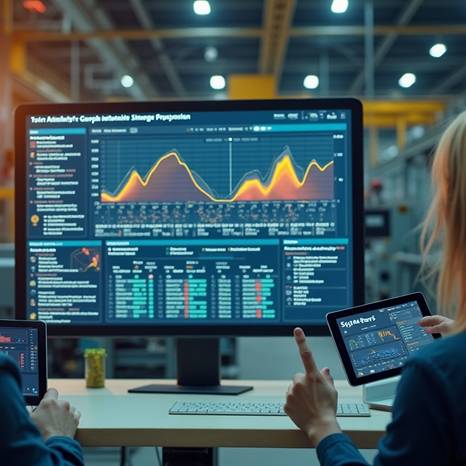
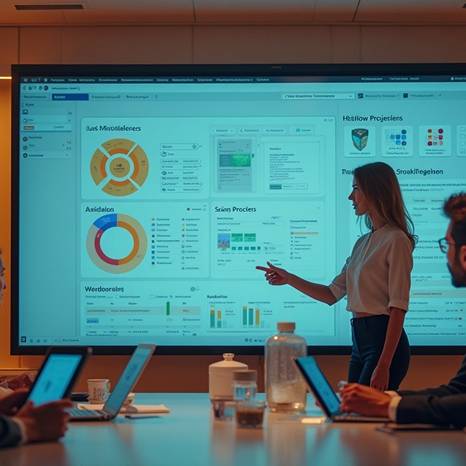
Proven Results
Our proprietary AI platform enhances every aspect of the production process with intelligent optimization and real-time adaptability
1,000 Prototypes in 48 Hours

David Martinez
Production Manager, ElectroCase Systems
45% faster production time on complex aluminum enclosures
“The AI-driven sheet metal fabrication process transformed our electronic housing production. The intelligent bend sequencing and optimized nesting layouts delivered perfectly formed enclosures with excellent fit and finish, accelerating our manufacturing timeline.”
Custom Medical Devices

Jennifer Lee
Quality Director, AeroTech Industries
99.2% first-time-right rate on precision stainless steel brackets
“The precision and consistency we’ve achieved with Wefab.ai’s sheet metal fabrication platform have been crucial for our aerospace components. The AI’s ability to maintain tight tolerances while optimizing material utilization has dramatically improved our production reliability.”
Diverse Range of Sheet Metal Services
CNC
Machining
High-precision milling, turning, and drilling for complex components.
Welding &
Brazing
MIG, TIG, arc welding, and brazing for structural and aesthetic joints.
Cutting &
Profiling
Laser, plasma, flame, and waterjet cutting for custom shapes and profiles.
Bending &
Rolling
Forming tubes, pipes, and plates into required geometries.
Structural
Fabrication
High-precision milling, turning, and drilling for complex components.
Assembly &
Integration
MIG, TIG, arc welding, and brazing for structural and aesthetic joints.
Surface
Finishing
Laser, plasma, flame, and waterjet cutting for custom shapes and profiles.
Prototyping &
Volume Production
Forming tubes, pipes, and plates into required geometries.
Ready to experience the future of precision sheet metal works?
Let our AI work for you and transform your manufacturing process with intelligent toolpaths and unmatched precision.
Frequently Asked Questions
How does AI improve the sheet metal works process?
Our AI optimizes nesting layouts, cutting paths, bend sequences, and tooling selection, reducing production times and enhancing part quality. It continuously learns from past operations to minimize material waste and predict optimal fabrication parameters for each design.
What materials can be processed?
The system works with a wide variety of sheet metal materials including mild steel, stainless steel, aluminum, copper, brass, galvanized steel, pre-painted steel, and specialty alloys. The AI automatically adjusts parameters for each material’s unique properties and thickness.
What are the typical turnaround times for sheet metal parts?
Simple components can be completed in 3-5 days, while complex assemblies requiring multiple processes and finishing may take 7-10 business days. For high-volume production, ongoing scheduled deliveries are available.
How is part accuracy ensured in sheet metal works?
The AI employs bend compensation, K-factor calculations, and material-specific forming parameters. Each component undergoes dimensional inspection, with capability for holding tolerances to ±0.005″ on critical features depending on material and geometry.
What file formats are accepted for sheet metal works projects?
The system accepts STEP, IGES, X_T, Parasolid, SolidWorks, and other standard CAD formats. The AI can also interpret GD&T callouts to ensure critical features meet specifications. For optimal results, sheet metal-specific features like bend lines should be clearly defined.
What thickness range can be accommodated?
The sheet metal equipment can process materials from 0.020″ (0.5mm) up to 0.5″ (12.7mm) depending on the material type. The AI selects the appropriate tooling and processes based on material gauge and properties.
What bend radius options are available?
A range of bend radii based on material thickness is available, typically from 0.030″ to 0.250″. The AI recommends the optimal bend radius for specific material and application to balance formability and structural integrity.
Are assembled sheet metal components available?
Yes, the AI coordinates the entire workflow including welding, hardware installation, and assembly operations. Purchased components, fasteners, and other elements can be integrated into final assemblies.
What finishing options are offered for sheet metal parts?
A complete range of finishing options is available including powder coating, wet painting, anodizing, plating, brushing, polishing, and silk screening. The AI helps select the optimal finish for aesthetic and functional requirements.
How are complex sheet metal assemblies handled?
The AI analyzes assembly requirements and sequences production steps for optimal results. The system manages spot welding, TIG/MIG welding, riveting, clinching, and other joining methods to produce complete assemblies from designs.