AI-Powered Metal Binder Jetting for Complex Metal Parts
AI-Powered Metal Binder Jetting for High-Volume Production and Complex Metal Parts
Our AI manages every step of the tool & die making process, delivering high-quality tooling faster and more efficiently than ever.
“Our AI-powered platform takes full control of your Metal Binder Jetting projects, acting as your dedicated Single Point of Contact. From optimizing print parameters to ensuring perfect sintering results, our AI works 24/7 to deliver precision components on time and within budget.”
End-to-End Production Management
Requirement Capturing
Our AI captures your project specifications through an intuitive interface, ensuring metal powder selection, tolerances, and surface finish requirements are understood from the start.
Automatic feature recognition and printing strategy selection
Metal Powder & Binder Selection
Our AI selects the optimal metal powder, binder type, and printing parameters based on part geometry, mechanical requirements, and production volume.
Intelligent saturation levels and binder-to-powder ratio optimization
Design for Binder Jetting
The AI optimizes your design for Metal Binder Jetting, analyzing features for printability, shrinkage compensation, and potential sintering challenges.
Real-time DfAM with shrinkage prediction and geometry optimization
Project Monitoring
Track Binder Jetting operations in real-time with AI-powered updates on print head performance, powder bed conditions, and green part integrity.
Live monitoring of binder deposition and powder spreading uniformity
Follow-ups & Reporting
Stay informed with automated follow-ups and detailed reports on material certification, dimensional inspection, and metallurgical verification.
Comprehensive first article inspection documentation
Quality Assurance
AI coordinates CMM inspection, density testing, and microstructure analysis, ensuring parts meet specifications with minimal deviation.
Automated shut height verification and parting line validation
Risk Analysis
The AI identifies production risks like binder migration, sintering distortion, or density variations and implements compensating strategies proactively.
Predictive simulation and printing parameter adjustments
Post-Processing Coordination
From depowdering and debinding to sintering and infiltration, the AI optimizes the post-printing workflow for speed and cost.
Seamless coordination of thermal processing and secondary operations
Why Choose Our
AI Platform
24/7 Production Capability
Our AI never sleeps, managing your Metal Binder Jetting projects across multiple machines and shifts.
Unmatched Efficiency
Optimized print parameters and build box utilization mean faster production and higher throughput.
Exceptional Precision
AI compensates for sintering shrinkage and material behavior, delivering tight tolerances consistently.
Cost-Effective Manufacturing
Smart powder management, optimized part nesting, and batch processing offer competitive pricing.
Proactive Solutions
Shrinkage variations, sintering distortion, and density inconsistencies are detected and addressed before they affect part quality.
Human Expertise When You Need It
Our experts complement AI capabilities with specialized knowledge and hands-on experience
Our experts complement AI capabilities with specialized knowledge and hands-on experience
- Complex project consultation and custom solutions design
- Technical support for specialized materials and finishing requirements
- Quality assurance reviews for critical applications
- On-demand engineering support and design optimization
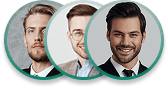
Meet Our Metal Binder Jetting Specialists and Sintering Engineers
20+ Years Combined Experience
Complex project consultation and custom solutions design
Technical support for specialized materials and finishing requirements
Quality assurance reviews for critical applications
On-demand engineering support and design optimization
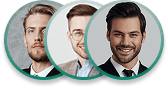
Meet Our Metal Binder Jetting Specialists and Sintering Engineers
20+ Years Combined Experience
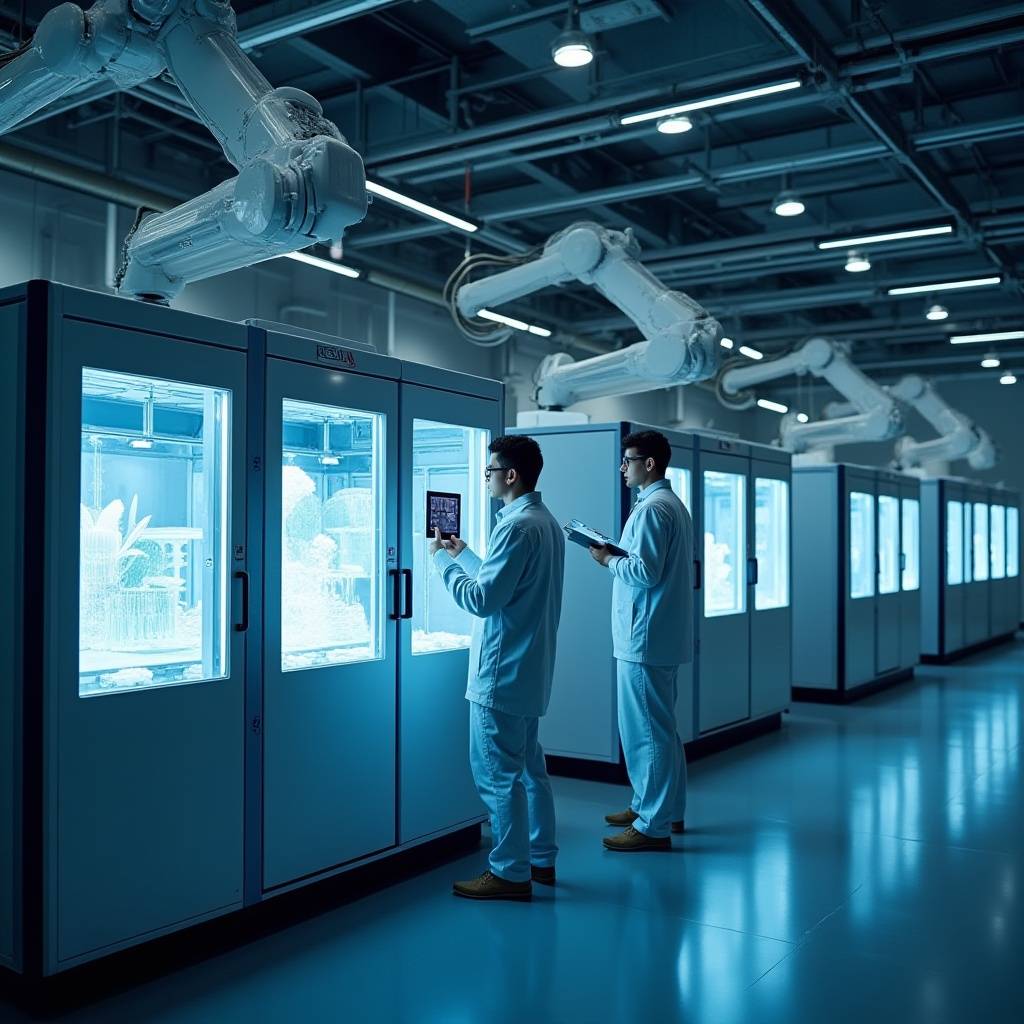
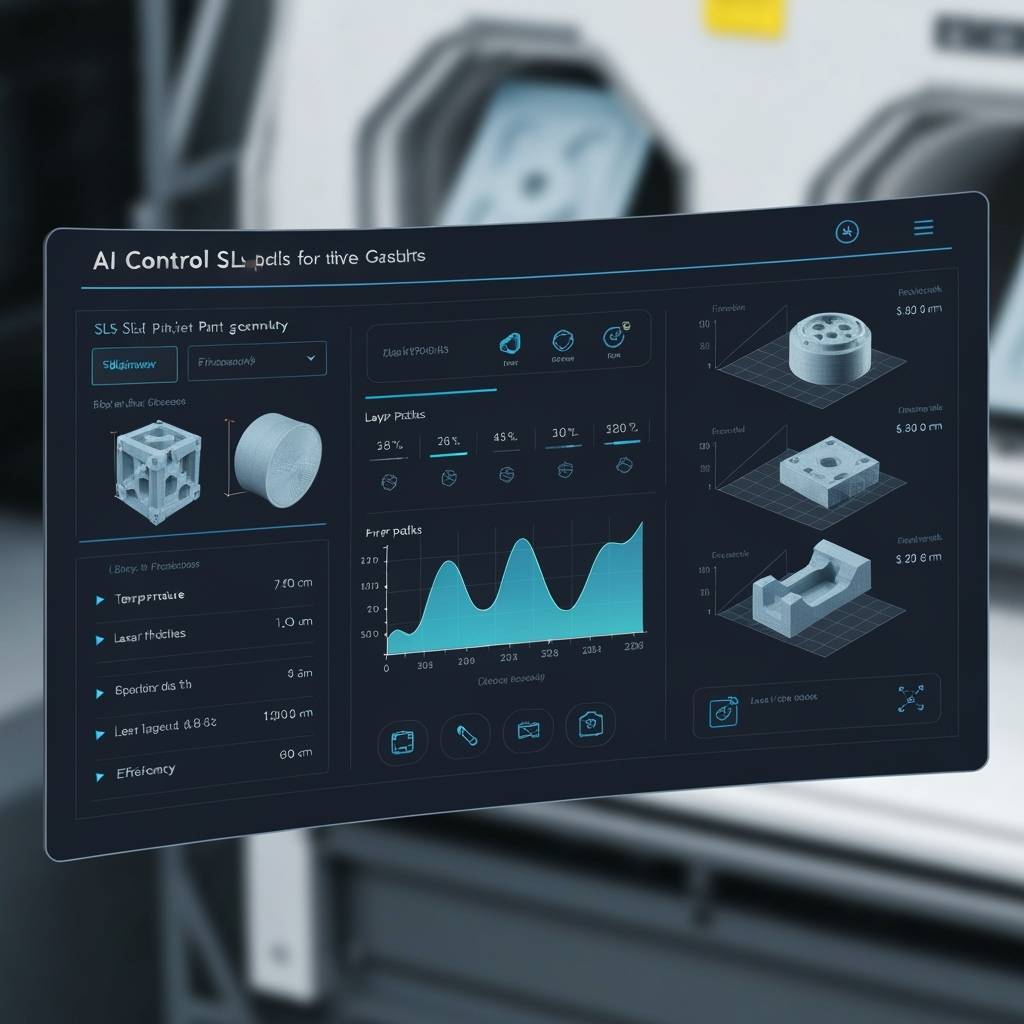
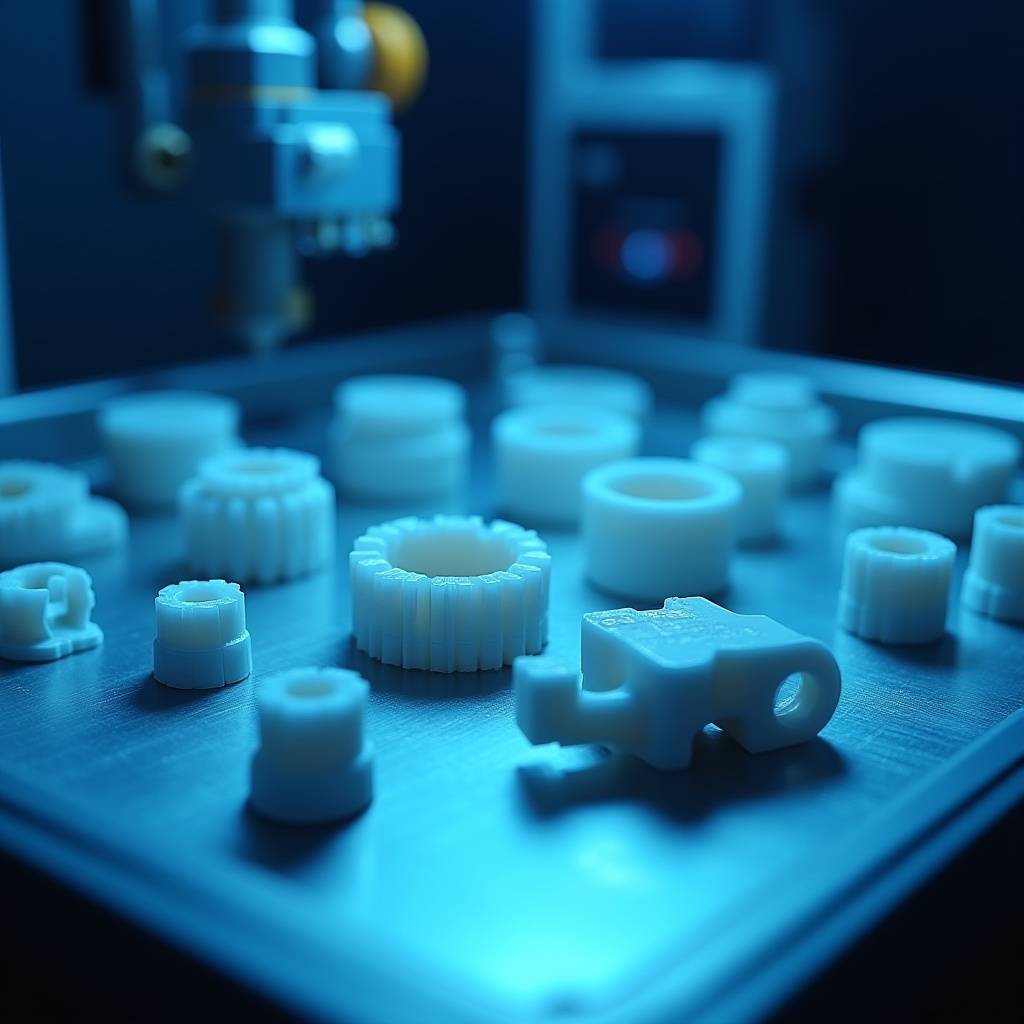
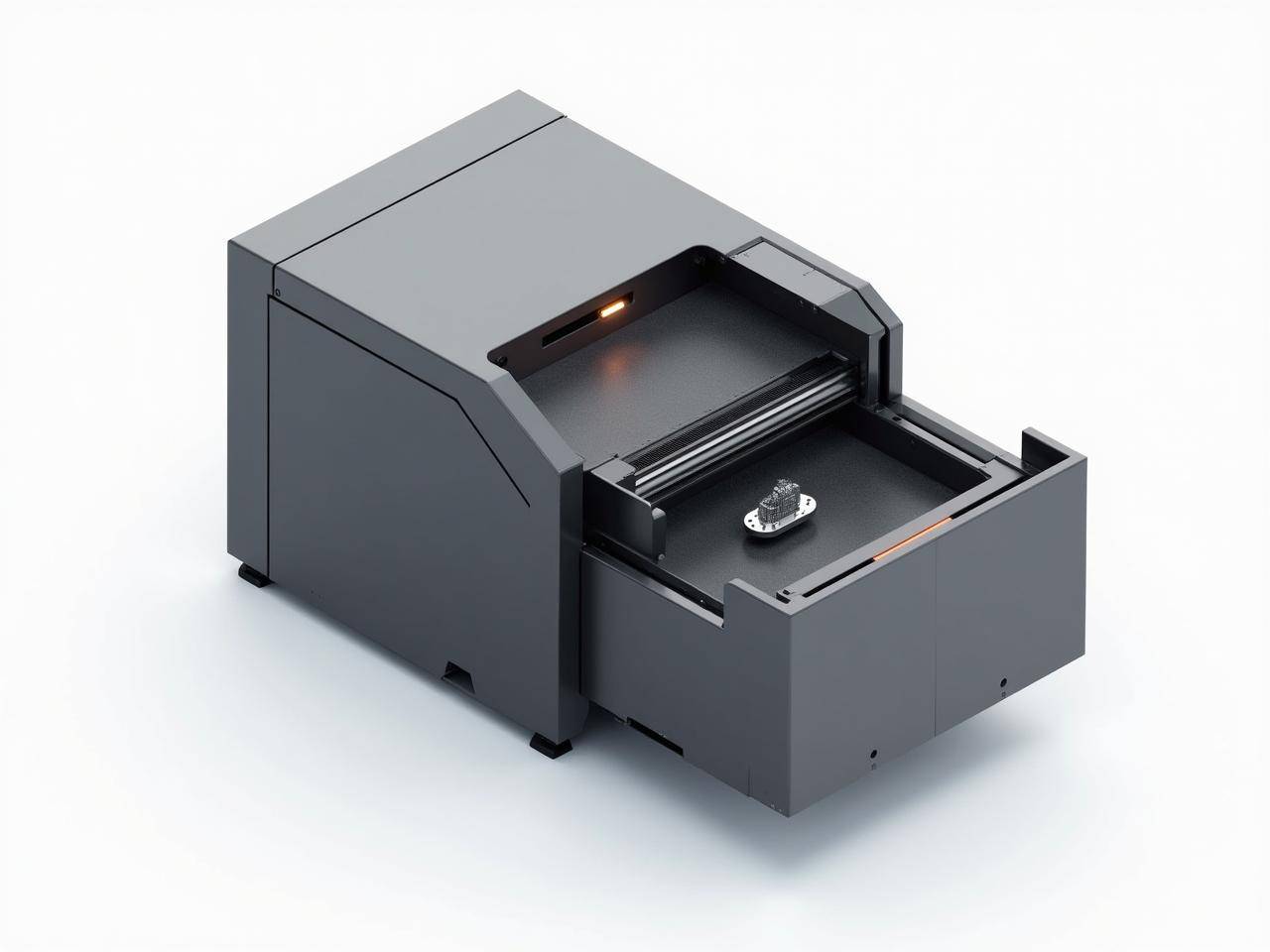
Proven Results
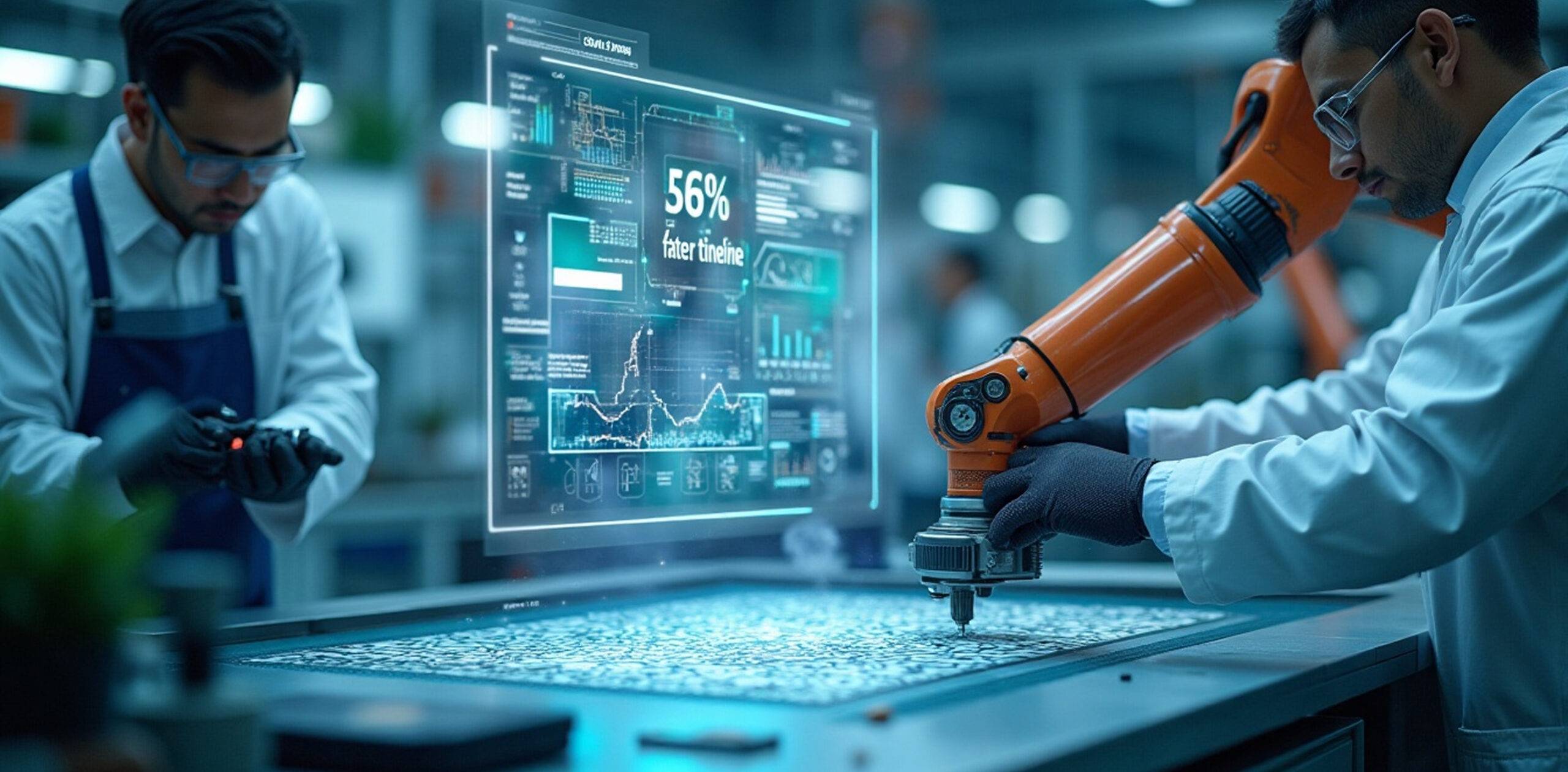
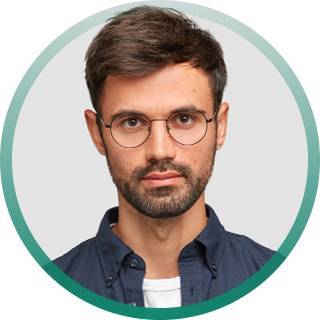
Company Name A
Production Manager, Industrial Hardware Solutions
45% higher production volumes on stainless steel components
The AI-driven Metal Binder Jetting process transformed our hardware component production. The intelligent shrinkage compensation and optimized sintering profiles delivered perfectly dimensioned parts with excellent material properties, accelerating our manufacturing timeline. Michael Torres, Production Manager, Industrial Hardware Solutions
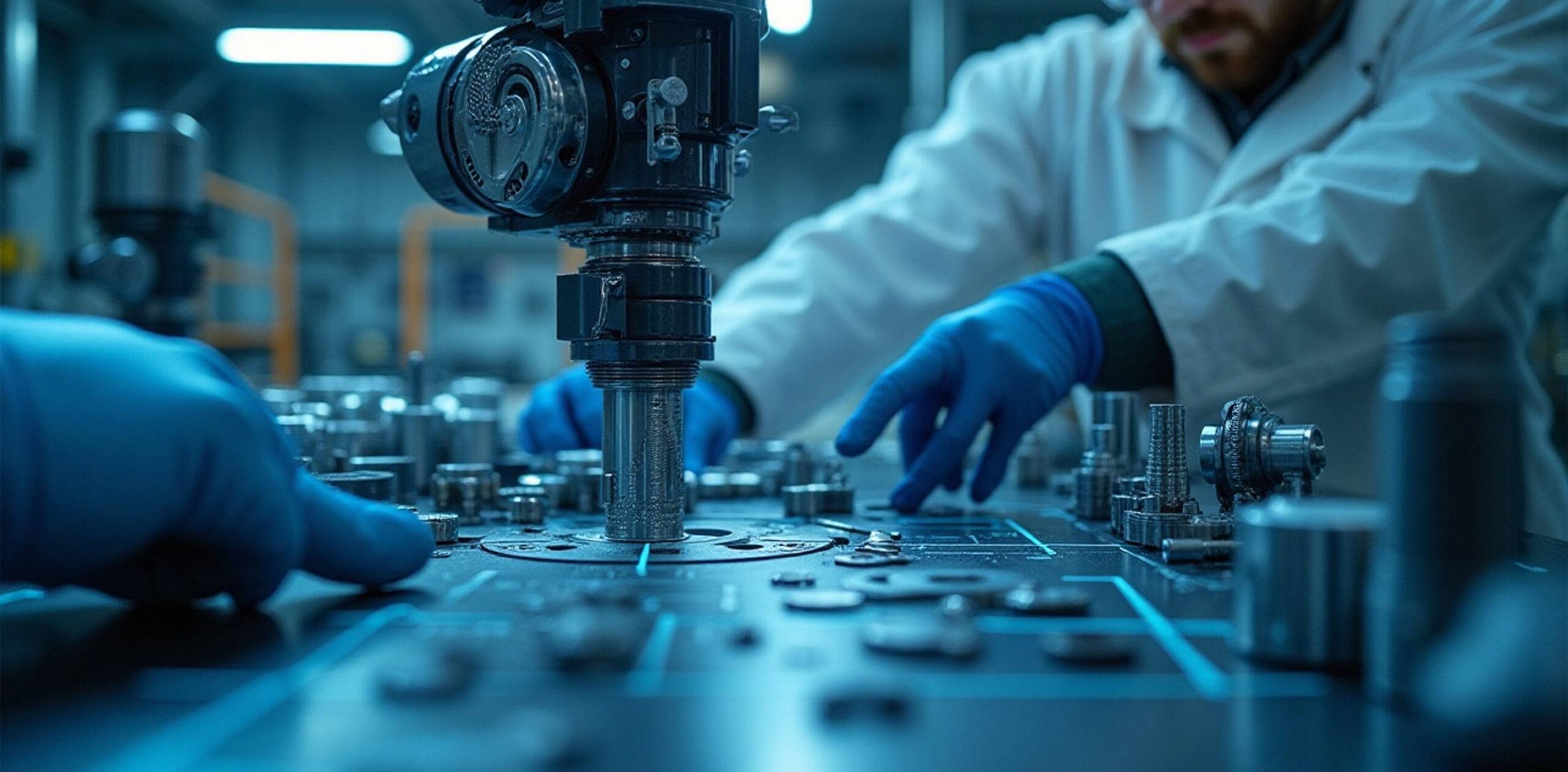
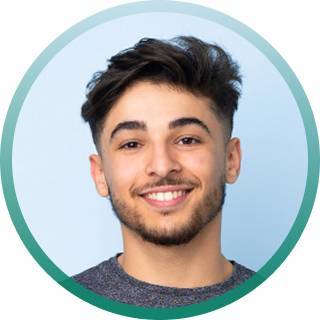
Company Name A
R&D Director, ThermalTech Innovations
99.2% first-time-right rate on complex copper heat exchangers
The precision and consistency we’ve achieved with Wefab.ai’s Metal Binder Jetting platform have been crucial for our thermal management devices. The AI’s ability to maintain tight tolerances while optimizing thermal processing has dramatically improved our production reliability. Dr. Katherine Wu, R&D Director, ThermalTech Innovations
Our 3d Printing Capabilities
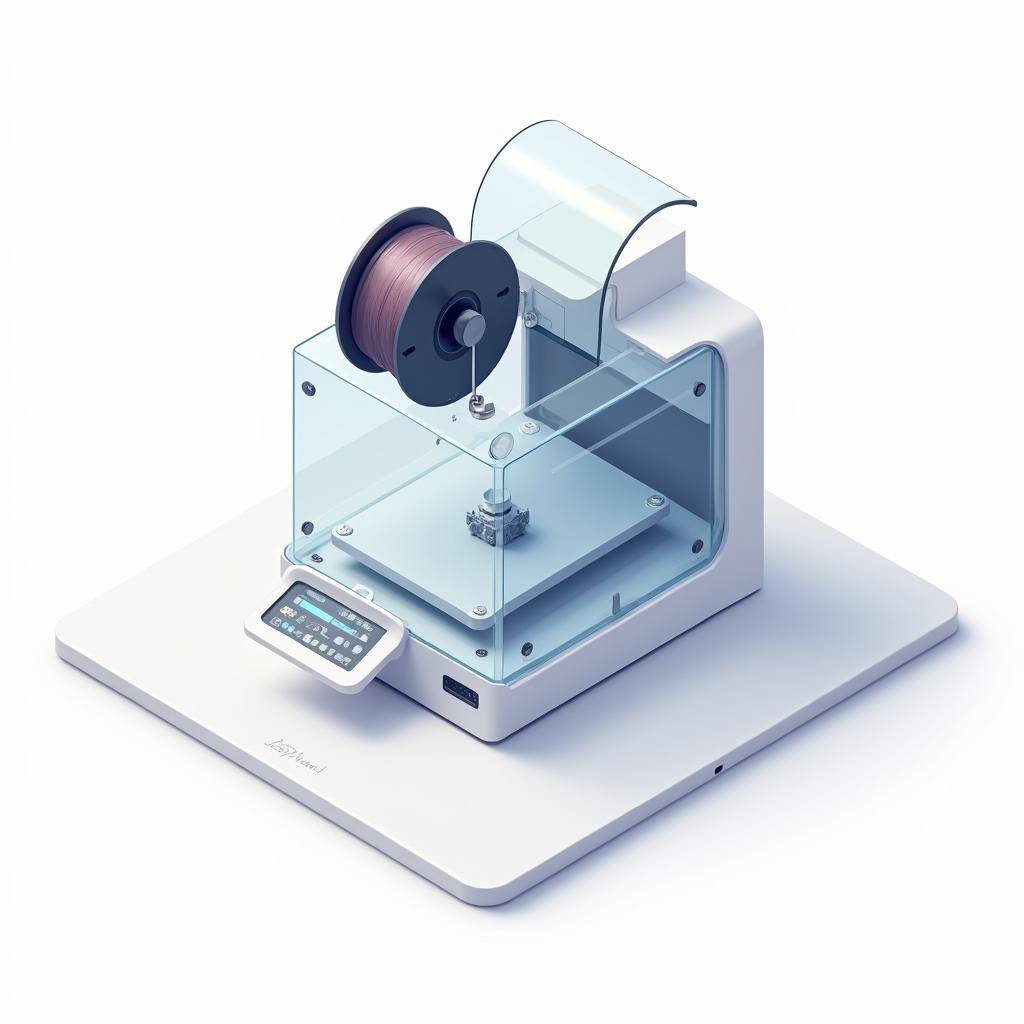
Plastic 3D Printing Service
Quick and cost-effective 3D printing solutions
- Precision level: ±0.5% with a minimum of 0.6 mm
- Turnaround: Starting from 2 business days
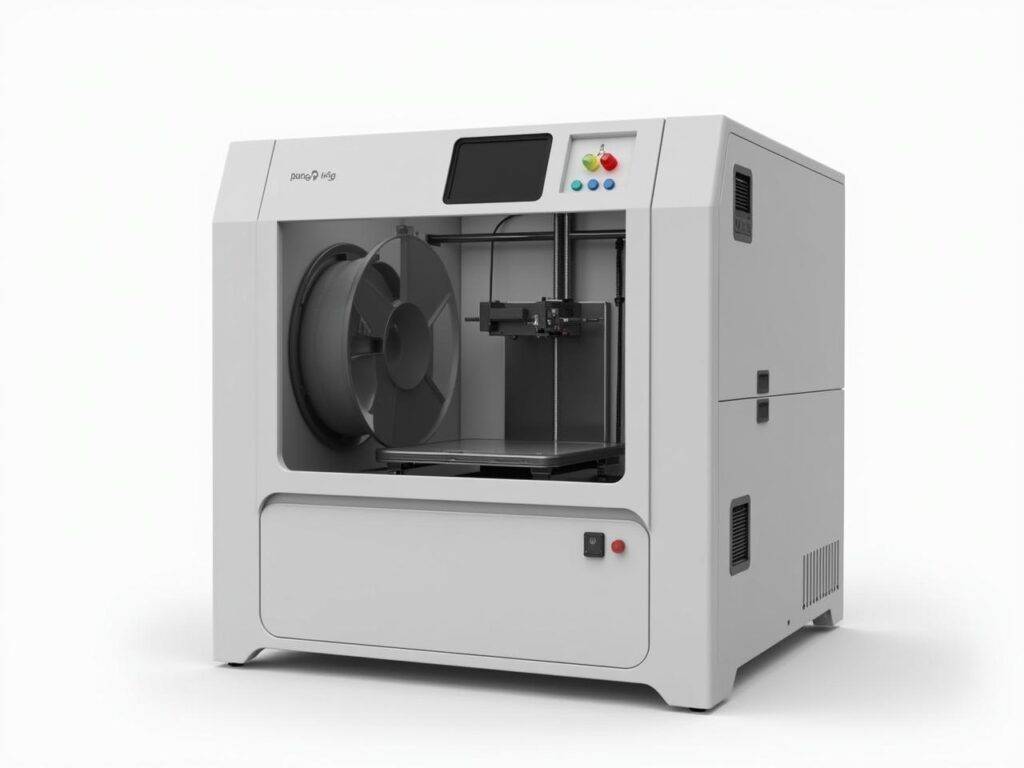
FDM 3D Printing
Efficient and budget-friendly prototyping
- Accuracy: ±0.5% with a minimum of 0.5 mm
- Delivery: As fast as 1 business day

Multi Jet Fusion
Robust prototyping and small-batch production
- Precision: ±0.3% with a minimum of 0.3 mm
- Lead time: From 2 business days
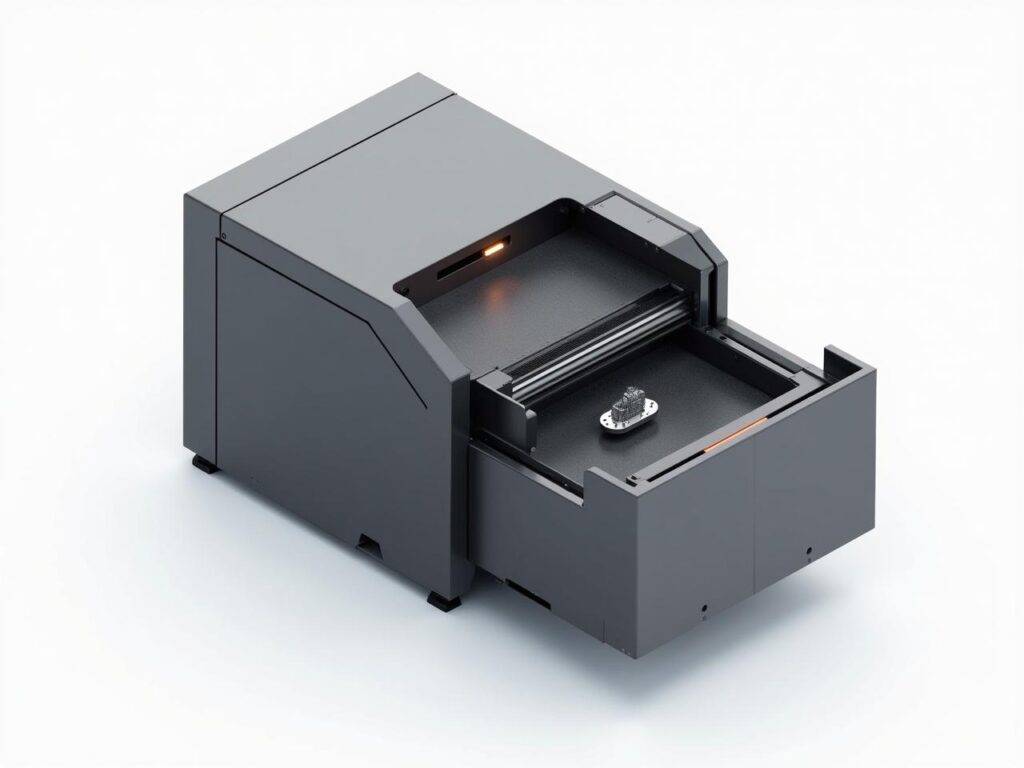
SLS 3D Printing
Durable and versatile printing options
- Tolerance: ±0.3% with a minimum of 0.4 mm
- Processing time: Starting from 3 business days
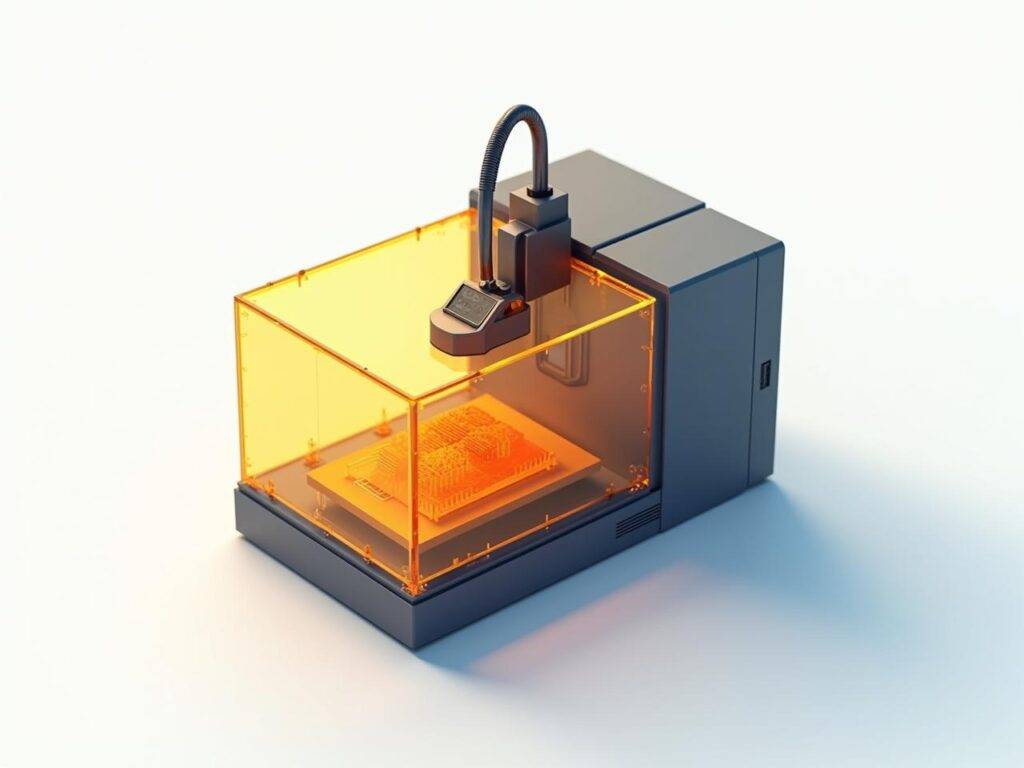
Stereolithography - SLA 3D Printing
High-detail visual prototyping
- Accuracy: ±0.3% with a minimum of 0.3 mm
- Turnaround: From 2 business days
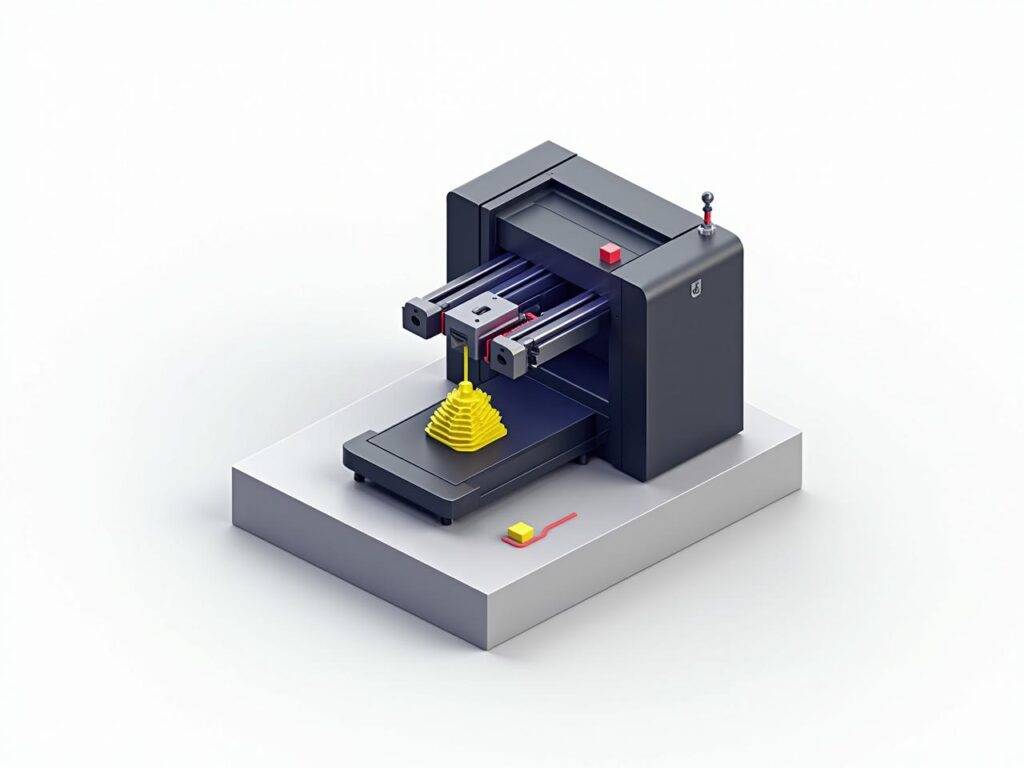
PolyJet 3D Printing
Precise and multi-material printing
- Dimensional accuracy: ±0.2% with a minimum of 0.2 mm
- Delivery: Starting from 2 business days
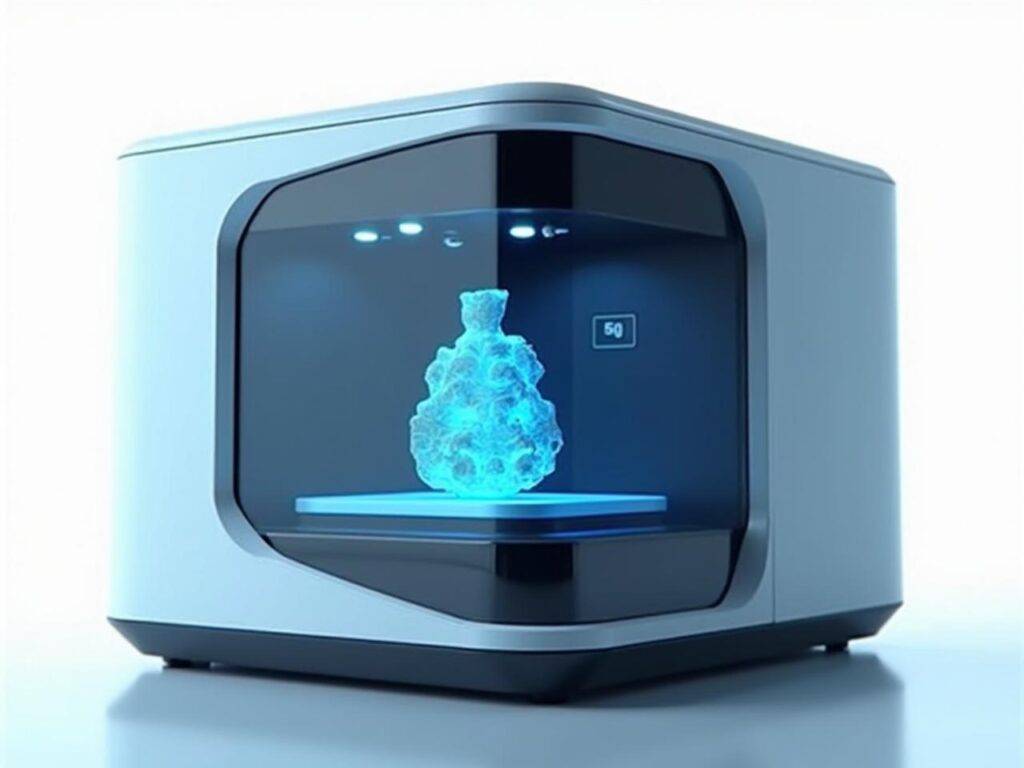
Carbon DLS
Fast and flexible production-grade parts
- Precision: ±0.4% with a minimum of 0.5 mm
- Lead time: From 3 business days
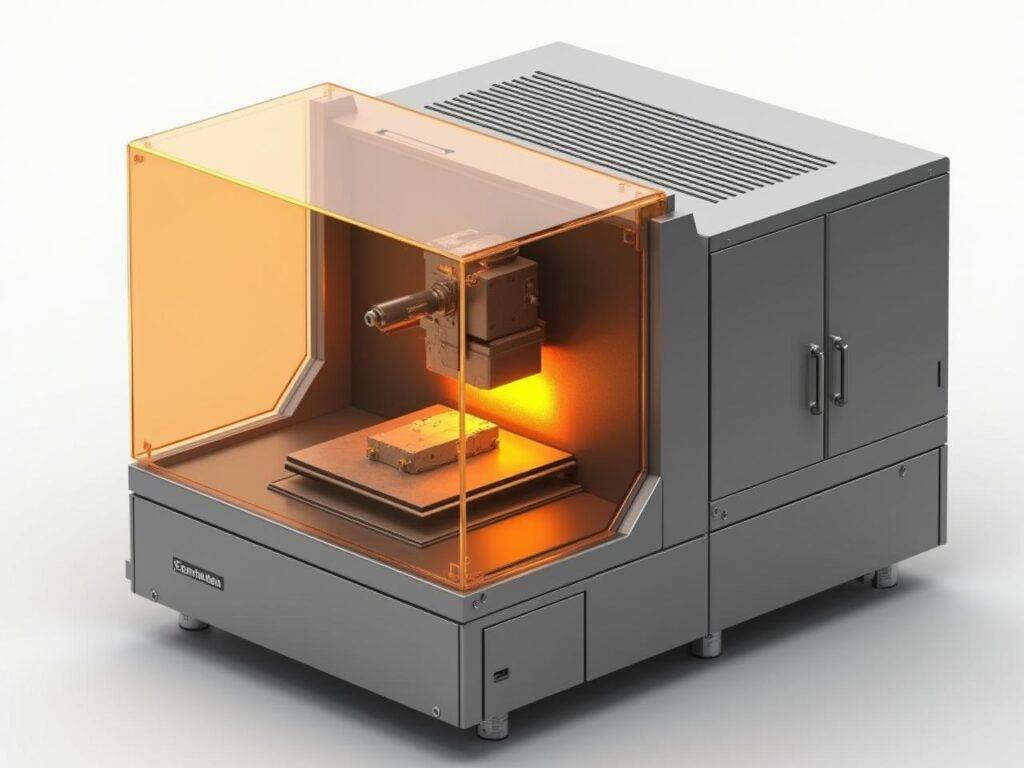
Metal 3D Printing Service
High-strength metal part fabrication
- Tolerance: ±0.3% with a minimum of 0.4 mm
- Turnaround: Starting from 4 business days
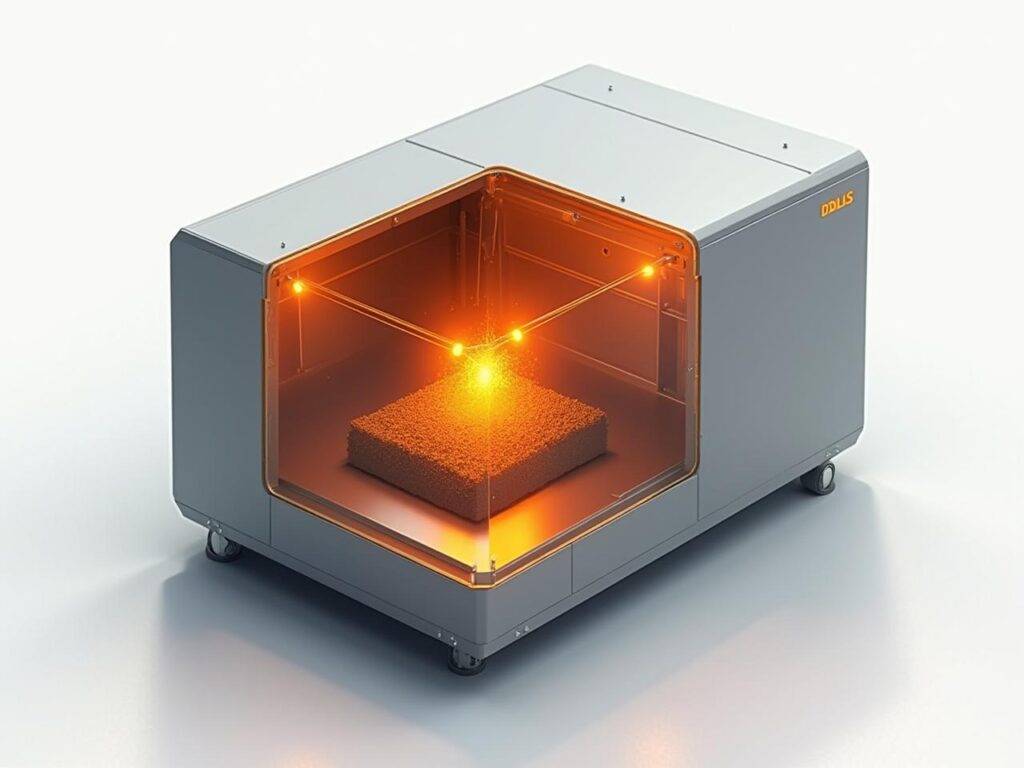
Direct Metal Laser Sintering
Advanced metal prototyping and production
- Accuracy: ±0.3% with a minimum of 0.3 mm
- Delivery: From 5 business days
Ready to experience the future of high-volume metal part production?
Let our AI work for you and transform your manufacturing process with intelligent Metal Binder Jetting strategies and unmatched throughput.
Frequently Asked Questions
How does AI improve the Metal Binder Jetting process?
Our AI optimizes binder saturation, print head parameters, and sintering profiles, increasing production throughput and enhancing part quality. It continuously learns from sintering data to minimize distortion and predict optimal processing parameters for each geometry.
What metal powders can you use in your Binder Jetting process?
At Wefab.ai we use a wide variety of metal powders for Binder Jetting including stainless steel (316L, 17-4PH), tool steels, copper, bronze, Inconel, tungsten carbide, and titanium. Our AI automatically adjusts printing parameters and sintering profiles for each powder’s unique properties.
What are your typical turnaround times for Metal Binder Jetted parts?
Simple components can be completed in 7-10 days, while complex parts requiring extensive sintering and infiltration may take 12-18 business days. For high-volume production, we offer ongoing scheduled deliveries.
How do you ensure part accuracy in Metal Binder Jetting?
Our AI employs predictive shrinkage compensation, controlled sintering cycles, and process parameter optimization. Each component undergoes dimensional inspection, with capability for holding tolerances to ±0.005″ on precision features depending on material and geometry.
What build volume can you accommodate with Metal Binder Jetting?
Our Metal Binder Jetting equipment can produce parts within a 400mm x 250mm x 250mm envelope in a single build. Multiple parts can be efficiently nested for high-volume production runs.
What post-processing is required for Metal Binder Jetted parts?
Metal Binder Jetted parts go through a multi-stage process including depowdering, debinding, sintering, and sometimes infiltration or Hot Isostatic Pressing. Our AI manages this workflow efficiently, including surface finishing and secondary operations when needed.
How does Metal Binder Jetting compare to other metal 3D printing technologies?
Metal Binder Jetting excels in high-volume production scenarios, offering lower per-part costs and faster throughput than laser-based processes. Our AI platform analyzes your design and production needs to determine if Binder Jetting offers advantages over DMLS or EBM for your specific application.
What is the minimum wall thickness for Metal Binder Jetted parts?
Our Metal Binder Jetting process can typically achieve wall thicknesses of 0.5mm and above, depending on material and geometry. Our AI analyzes your design to ensure all features meet printability requirements.
Can Metal Binder Jetting produce fully dense metal parts?
Metal Binder Jetted parts typically achieve 96-99% density after sintering. For applications requiring maximum density, we incorporate infiltration or Hot Isostatic Pressing to approach 100% density in the final parts.
What file formats do you accept for Metal Binder Jetting projects?
We accept STL, STEP, IGES, X_T, Parasolid, SolidWorks, and other standard CAD formats. Our AI can also interpret GD&T callouts to ensure critical features meet specifications.